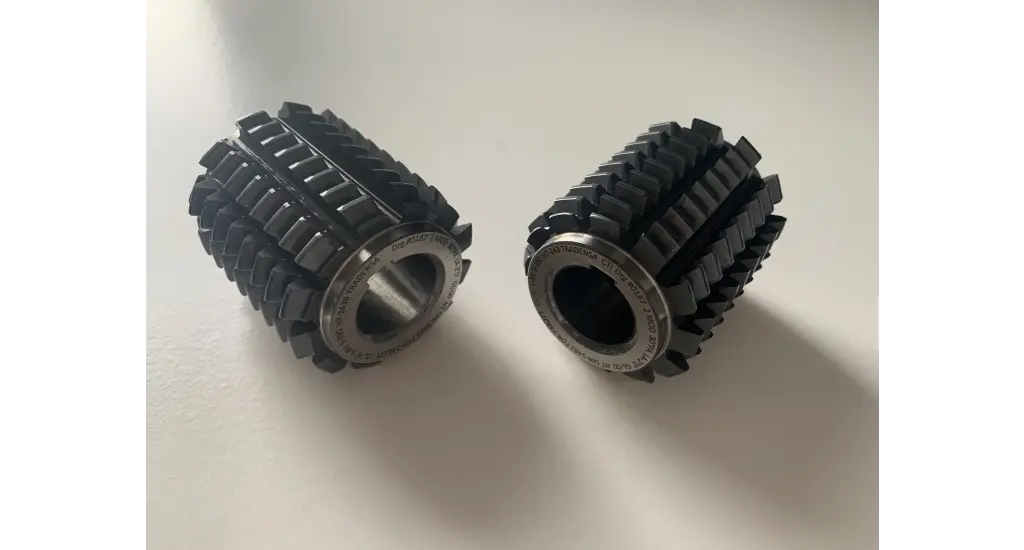
Jakie są zalety powłok i pokryć wykorzystywanych w produkcji narzędzi skrawających do kół zębatych i wielowypustów?
Powłoki (pokrycia) są wykorzystywane w obróbce skrawaniem ze względu na znaczną poprawę właściwości skrawających oraz trwałości narzędzi. Aktualnie nanosi się powłoki na praktycznie wszystkie narzędzia, nawet na materiały supertwarde (np. węglik spiekany).
Narzędzia do kół zębatych takie frezy ślimakowe, frezy krążkowe, dłutaki Fellowsa, przeciągacze oraz noże do kół stożkowych nie są tutaj wyjątkiem.
Celem nanoszenia powłok jest wydłużenie żywotności narzędzia, w tym również narzędzi do kół zębatych, ponieważ prowadzi to do:
- zmniejszenia współczynnika tarcia w strefie kontaktu narzędzia, wióra oraz przedmiotu obrabianego,
- zwiększenia twardości warstwy wierzchniej w narzędziu,
stworzenie bariery ochronnej zmniejszającej przenikanie ciepła w głąb materiału
ograniczenie dyfuzji, - ograniczenia powstawania zmian chemicznych w warstwach wierzchnich narzędzia.
Innymi zaletami są np. zmniejszenie składowych siły całkowitej, obniżenie temperatury skrawania, zmniejszenie skłonności do narostu, zmniejszenie chropowatości powierzchni obrobionej, ułatwienie ucieczki wióra w rowkach wiórowych. Powyższe czynniki wpływają albo na dłuższą trwałość narzędzia albo na okresowe zwiększenie prędkości skrawania. Dodatkowym plusem takiego rozwiązania jest możliwość wizualnej oceny stanu zużycia narzędzia. Jeżeli barwa mocno różni się od tej w miejscach niepracujących wiadomo, że zużycie jest już znaczące.

Rys. 1 Podział powłok na narzędzia skrawające [1]
Rys. 1 przedstawia podział powłok nanoszonych na narzędzia skrawające. Głównym elementem pod kątem narzędzi do uzębień są powłoki supertwarde CVD-PVD.
Metody wykonywania pokryć na narzędzia skrawające do kół zębatych i wielowypustów
Metoda fizycznego odsadzania PVD (ang. Physical Vapour Deposition) – odbywa się w temperaturze do 550 ℃ co skutkuje pozytywnym brakiem odpuszczenia zahartowanej stali.
Jest to najczęstsza metoda pokrywania frezów ślimakowych, dłutaków Fellowsa, przeciągaczy, frezów krążkowych oraz noży i głowic do kół stożowych. Etapy procesu:
- oczyszczenie powierzchni za pomocą obróbki strumieniowo-ściernej,
- umycie narzędzia w specjalnych roztworach i myjni ultradźwiękowej,
- usunięcie starej powłoki poprzez kąpiel w wodzie utlenionej lub w przypadku węglika elektrochemiczne roztwarzanie,
- ułożenie wsadu na stelażach w przestrzeni roboczej,
- odgazowanie wsadu,
- umieszczenie stelażu w komorze powlekającej oraz napełnienie jej argonem,
- wytworzenie próżni oraz podgrzanie w zależności od typu nanoszonej powłoki do temperatury 250-550 ℃,
- proces trawienia jonowego powierzchni powlekanych narzędzi – jej oczyszczenie i pobudzenie atomów przypowierzchniowych do łatwiejszej, dalszej dyfuzji,
- podgrzanie tarcz wykonanych z materiału stanowiącego warstwę powłoki (np. TiN) poprzez łuk elektryczny, w celu odparowania materiału tarczy,
doprowadzenie gazów reaktywnych (np. O2, N2) w celu wytworzenia odpowiednich związków z materiałem odparowanym, - chłodzenie i opróżnienie komory,
- jeżeli wymagana obróbka wygładzająca, tzw. mikropiaskowanie.
Proces nanoszenia powłok trwa od kilku do kilkunastu godzin, jej grubość to od 4 do 6 μm z kontrolą procesu do 0,25μm. Przy powyższej grubości i bardzo cienkiej warstwie powłoka praktycznie nie zmienia grubości narzędzia, jedynie delikatnie zaokrągla krawędź skrawającą [1].
Metoda chemicznego odsadzania CVD (ang. Chemical Vapour Deposition) – metoda chemicznego osadzania warstw z faz gazowych.
Etapy procesu:
- podgrzanie komory do wymaganej temperatury,
- podgrzanie parownika,
- dostarczenie gazów wspomagających proces nanoszenia,
- wytworzenie wyładowań jarzeniowych,
- doprowadzenie do komory gazów reaktywnych (np. O2, N2),
- odparowanie TiCl4 w parowniku,
- reakcje chemiczne zależne od temperatury procesu i końcowo uzyskanej warstwy,
- kontrola procesu i sterowanie skutkujące osadzenie warstw w określonej kolejności oraz grubości.
Początkowo metoda CVD wymagała użycia wysokich temperatur (1170-1370 K, około 900-1100 ℃) co skutkowało brakiem możliwości użycia na stalach szybkotnących ze względu na samoczynny proces odpuszczania.
W ostatnim czasie opracowano jednak technologię PACVD (Plasma Assited Chemical Vapour Deposition) wykorzystującą wyładowania jarzeniowe wraz z niskotemperaturową plazmą. Obniżono ciśnienie podczas nanoszenia powłok do 1-13hPa oraz przede wszystkim temperaturę, wynoszącą aktualnie 720-820K (450-550 ℃) przy zachowaniu dużej wydajności oraz jakości nanoszonych powłok [1].
Porównanie obu metod zostało przedstawione na rysunku 2. Zdecydowanie korzystniej pod kątem naprężeń w warstwie wierzchniej wypada metoda PVD. Posiada ona w przeciwieństwie do metody CVD naprężenia ściskające, które blokują rozprzestrzeniane się mikroszczelin.

Najczęściej stosowaną dzisiaj powłoką na frezy ślimakowe jest Alcrona Pro. Powłoka TiN była jedną z pierwszych powłok, następnie wymyślono powłokę TiAlN (tzw. Futurę Nano Top), jednak obie ze względu na niższą maksymalną temperaturę pracy wypadają mniej korzystnie w porównaniu z Alcroną Pro. Alcrona Pro została opracowana przez firmę Oerlikon Balzers, jej odpowiednikiem dającym w praktyce często podobny efekt jest pokrycie Exxtral-Plus od firmy Eifeler, jej właściwości zostały pokazane w tabeli na rysunku 4.

Rys. 3 Właściwości poszczególnych powłok firmy Oerlikon Balzers [1]


Rys. 5 Porównanie trwałości różnych powłok, w tym powłoki Exxtral-Plus oraz TiAlN w procesie wiercenia z różnymi prędkościami skrawania [2]

Rys. 6 Porównanie średniego wzrostu trwałości freza ślimakowego w zależności od użytej powłoki wg firmy Koepfer [16]

Jak widać na rysunkach 5, 6 oraz 7, wybór odpowiedniej powłoki ma bardzo duży wpływ zarówno na możliwe do osiągnięcia prędkości skrawania, jak i na trwałość narzędzia. Na rysunku 5 zostało przedstawione porównanie trwałości narzędzi w przypadku wiercenia tym samym narzędziem w jednym typie materiału (1.2311) z prędkością skrawania vc=80m/min oraz vc=160m/min. Widać tutaj wyraźnie zależność, że zastosowane pokrycie wyraźnie zwiększa trwałość narzędzia wraz ze wzrostem prędkości skrawania. Rysunek 6 przedstawia natomiast średni wzrost trwałości narzędzia w zależności od użytej powłoki. Obecnie, bardzo często stosowaną powłoką jest Alcrona Pro lub powłoka Exxtral-Plus.
Wniosek jest prosty, narzędzia do kół zębatych nie mają innych właściwości od standardowych narzędzi skrawających i jeżeli budżet pozwala oraz produkcja nie należy do jednostkowej to należy je każdorazowo pokrywać.
Frezy ślimakowe, frezy krążkowe, dłutaki Fellowsa i noże do kół stożkowych oraz przeciągacze ze stali szybkotnących HSS M2 i HSSe M35 zazwyczaj pokrywa się TiNem, natomiast te same narzędzia wykonane ze stali proszkowej oraz węglika spiekanego zalecamy pokrywać Alcroną Pro.
Jeżeli szukasz narzędzi do kół zębatych, które pokryte będą pracować trwale i niezawodnie to jesteś we właściwym miejscu:
- frezy ślimakowe -> znajdziesz tutaj
- frezy krążkowe -> znajdziesz tutaj
- dłutaki Fellowsa -> znajdziesz tutaj
- dłutaki na płytki -> znajdziesz tutaj
- przeciągacze i przepychacze -> znajdziesz tutaj
Frezarki obwiedniowe CNC -> znajdziesz tutaj
Ponadto posiadamy w ofercie również sprawdziany do wielowypustów, gwintów i otworów -> znajdziesz je tutaj oraz oprawki napędzane do frezowania obwiedniowego, nacinana kół stożkowych o zębach prostych czy Power Skivingu -> znajdziesz tutaj
Źródła:
1. Cichosz P., Narzędzia skrawające, WNT, Warszawa, 2006, ISBN 83-204-3181-6
2. http://www.eifeler.com/de/, 16:40, 16.10.2018
3. https://www.oerlikon.com/balzers/com/en/, 16:50, 16.10.2018
4. https://www.lmt-tools.com/fileadmin/user_upload/content_lmt-tools/content/segmente/verzahnen/downloads/LMT-Tools-Katalog-Verzahnen-s.pdf, 17:10, 18.10.2018