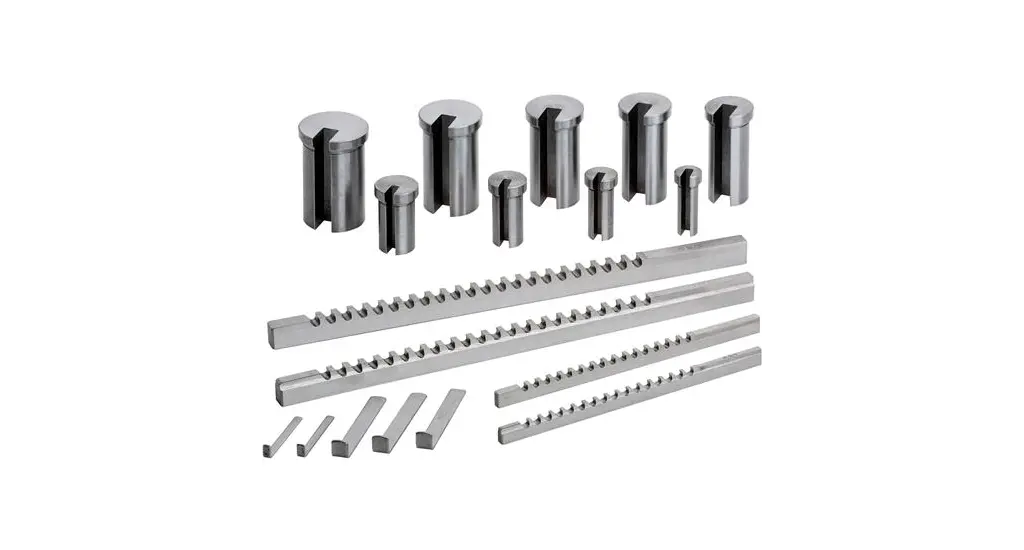
Co to jest przeciąganie? Co to jest przeciągacz?
Przeciąganie to proces obróbki skrawaniem polegający na nacinaniu, najczęściej kształtów wewnętrznych, narzędziem z odpowiednio ukształtowanymi ostrzami.
Istnieje wiele odmian przeciągania, ale najczęściej stosowanym jest przeciąganie prostoliniowe na nieruchomej części obrabianej.
Przeciąganie przeciągaczami jest procesem dedykowanym, tzn. każdy otwór czy kształt o danych wymiarach musi być obrabiany dedykowanym przeciągaczem.
Przeciągacz ze względu na rodzaj obróbki (ciągnięcie) ma specjalny chwyt, który jest mocowane w uchwycie przeciągarki. Narzędzie jest wprawiane w ruch prostoliniowy generujący siły skrawania. Część skrawająca (robocza) przeciągacza składa się przeważnie z trzech ostrzy:
- Ostrza zdzierające (część przeciągacza odpowiedzialna za obróbkę zgrubną.
- Ostrza wykończeniowe (część przeciągacza odpowiedzialna za obróbkę wykańczającą, na dany wymiar oraz tolerancję).
- Ostrza zapasowe
Ostrza zapasowe pełnią ważną funkcję. Przeciągacze jak każde narzędzie skrawające ulega podczas obróbki zużyciu. Ostrza przeciągaczy są ostrzone, przez co zmniejszają swoje wymiary. Po kolejnych regeneracjach ostrza zapasowe przejmują funkcję ostrzy wykończeniowych i pozwalają na dalszą obróbkę danej części w wymaganej tolerancji.
Na końcu przeciągacza wykonane jest tzw. prowadzenie tylne zgodne z wymaganym, końcowym kształtem, zapobiega ono powstawaniu błędów w końcowej fazie przeciągania.
Przeciągacze do części wewnętrznych mogą być ponadto okrągłe lub płaskie (najczęściej do przeciągania rowków wpustowych lub pojedynczych kształtów).

Budowa przeciągacza do otworów
Kierunek ruchu przeciągaczy
Kierunek ruchu przeciągaczy zależy od typu obrabiarki (przeciągarki) jaka jest używana. Przeciągarki dzielimy na dwa rodzaje:
- przeciągarki pionowe (bardziej popularne) – hydrauliczne lub elektromechaniczne
- przeciągarki poziome (mniej popularne) – hydrauliczne
W pionowych przeciągarkach ruch następuje zazwyczaj do dołu, ale możliwe jest również jego odwrócenie.
Po zamocowaniu przeciągaczy w maszynie, przeciągacz jest wprawiany w ruch prostoliniowy. Część z otworem wstępnym ustawia się samoczynnie (nie jest ona na stałe zamocowana) oraz jest dociskana siłą skrawania do płyty oporowej przeciągarki.
Przeciągacze do otworów i kształtów wewnętrznych (np. przeciągacze do wielowypustów ewolwentowych) wykonane są z jednego kawałka materiału, są to tzw. przeciągacze monolityczne.
Inaczej sytuacja się przedstawia w przypadku przeciągaczy zewnętrznych, tutaj przeciągacze są zazwyczaj płaskie oraz montowane na płytę suportu i niekoniecznie muszą być monolityczne. W przypadku powierzchni zewnętrznych zamkniętych składa się z segmentów skrawających o uzębieniu wewnętrznym mocowanych i ustalanych na korpusie przeciągarki. W takim wypadku ruch główny wykonuje przeciągacza część.
Przeważnie w przeciąganiu mówimy tylko o ruchu prostoliniowym, jednak istnieje jeszcze specjalny typ uzębień wymagający bardziej złożonych ruchów, jest nim przeciąganie uzębień lub rowków śrubowych.
Kolejne ostrza przeciągacza są w takim przypadku wykonane śrubowo o kącie 90 ° – α, gdzie α to kąt pochylenia linii śrubowej przeciąganej części. W przypadku części z rowkami, uzębieniami i wielowypustami śrubowymi mamy dwie składowe ruchu, które mogą być wykonywane przez narzędzi lub przedmiot lub poprzez rozdzielenie między oba.

Przeciągacze płaskie, tuleje oraz podkładki do przeciągania rowków wpustowych
Zasady projektowania przeciągaczy – warunki przeciągania
Zaprojektowanie operacji przeciągania to głównie zaprojektowanie zgodnego narzędzia. Przeciągacze są narzędziami specjalnymi:
- Zarys ma określone kształty, wymiary oraz tolerancję
- Różna jest długość przeciągania
- Różne są typy maszyn i uchwytów
- Część może mieć różny materiał
W przypadku przeciągaczy niestety rzadko się zdarza, żeby jeden przeciągacz mógł zostać użyty do wielu części.
Przy konstrukcji przeciągacza jednym z ważniejszych elementów jest dobór grubości warstwy skrawanej. Proces przeciągania charakteryzuje się znacznie mniejszymi grubościami warstwy skrawanej niże pozostałe procesy obróbki skrawaniem.
Wybór grubości warstwy skrawanej zależy od kilku czynników:
- Czy ostrza są zdzierające czy wykończeniowe.
- Pojemności rowków międzyzębnych, których zadaniem jest pomieszczenie wiórów.
- Maksymalna siła przeciągania – zależna od minimalnego przekroju przeciągacza
Należy pamiętać, że małe wartości grubości warstwy skrawania sprzyjają większej dokładności i lepszej chropowatości powierzchni w przeciąganej części.
Dla ostrzy zdzierających zaleca się grubość warstwy skrawanej w zakresie 0,1-0,25mm, w przypadku ostrzy wykańczających 0,03-0,1mm. Mniejsze wartości dla przeciągania wykańczającego mogą powodować ślizganie po powierzchni zamiast skrawania. Poza ostrzami wykańczającymi przeciągacz może mieć również ostrza nagniatające, których zadaniem jest wygładzenie powierzchni po przeciąganiu.
Pojemność rowków międzyzębnych jest również ważną konstrukcyjnie częścią w projektowaniu przeciągaczy oraz procesu przeciągania. W celu ułatwienia odprowadzania wiórów z przestrzeni międzyzębnej, bardzo często stosuje się na krawędziach skrawających rowki dzielone. Pozwalają one na łatwiejsze i płynniejsze usuwanie wiórów podczas przeciągania.
Ostatnim elementem jest siła przeciągania. Siłę przeciągania należy rozpatrywać zarówno pod kątem siły w posiadanej przeciągarce jak i pod kątem twardości oraz wytrzymałości na rozciąganie w materiale części. Przebieg siły skrawania jest zależny od liczby równocześnie pracujących oraz nowo wchodzących ostrzy. Siła przeciągania potrafi rosnąć skokowo ze ponieważ średnia liczba jednocześnie pracujących ostrzy nie jest liczbą całkowitą.
Parametry skrawania oraz dobór chłodziwa w procesie przeciągania
Prędkość skrawania w przeciąganiu – dobór odpowiedniej prędkości skrawania w procesie przeciągania jest bardzo istotną częścią procesu. Przeciąganie składa się z dwóch faz, ruch obróbczy oraz ruch powrotny. Prędkość skrawania musi pozwolić na płynną oraz szybką obróbkę oraz jednocześnie na wysoką międzyostrzeniową trwałość przeciągacza i jego nieuszkodzenie. Przeciągacze wykonane są zazwyczaj ze stali szybkotnącej HSS-M2, stali szybkotnącej HSSe-M35 lub stali proszkowych. Ewentualne uszkodzenie lub zniszczenie przeciągacza poprzez zbyt wysokie parametry skrawania jest bardzo kosztowne. Materiał oraz prędkość skrawania w przeciąganiu dobiera się względem wymaganej chropowatości części oraz jej materiału. Im twardsza część, tym wyższe prędkości skrawania. Przy przeciągacz z wkładkami węglikowymi możliwe jest nawet przeciąganie z prędkością do 40m/min.
Dobór cieczy obróbkowej – przeciąganie jest wykonywane głównie na morko, chociaż na sucho jest również możliwe. Sugerujemy przeciąganie na mokro, ponieważ zwiększa ono trwałość ostrzy oraz zmniejsza chropowatość przeciąganej powierzchni. Przy małych prędkościach skrawania zalecamy oleje obróbkowe (prędkość skrawania Vc < 10 m/min), a przy wyższych (Vc > 10 m/min) emulsje olejowe 10-20%.
Zużycie ostrzy i ostrzenie przeciągaczy
Przeciągacze jak każde narzędzie skrawające podczas pracy ulegają stępieniu. Im więcej części zostaje przeciągnięte, tym generowane są większe siły skrawania oraz gorsza chropowatość powierzchni. Zużycie ostrzy w przeciągacza rozpatruje się pod dwoma kątami:
- VB – starcie na powierzchni przyłożenia
- Rn – promień zaokrąglenia krawędzi skrawającej
W praktyce rozpatruje się tylko VB i ostrza przeciągacza należy ostrzyć co VB=0,2-0,4mm (najlepiej 0,2-0,25mm). W ten sposób możliwe jest zachowanie stałej chropowatości powierzchni oraz zmniejszenie sił skrawania podczas procesu przeciągania.
Stępione ostrza przeciągacza należy dokładnie naostrzyć od strony powierzchni natarcia.

Proces ostrzenia przeciągaczy o rowkach spiralnych
Klasa wykonania uzębienia po przeciąganiu oraz trwałość i żywotność przeciągaczy
Przeciąganie należy do procesów obróbki bardzo szybkiej i jest stosowane przeważnie w produkcji średnioseryjnej, wysokoseryjnej i masowej. Przeciąganie pozwala na osiągnięcie do 5 klasy wykonania uzębienia wg normy DIN oraz chropowatości powierzchni do Ra = 0,32 μm.
Prawidłowo używany przeciągacz pozwala w zależności od wielu czynników na przeciągnięcie międzyostrzeniowo nawet do 1.000-10.000 sztuk części, a do całkowitego zużycia przeciągacz można naostrzyć 10 do 15 razy.

Przeciągnięty wielowypust ewolwentowy
Dobór materiału przeciągacza oraz jego pokrycia
Materiał przeciągacza jest dobierany w zależności od twardości przeciąganej części oraz jej wytrzymałości na rozciąganie. Dla części miękkich przeciągacze wykonane są głównie ze stali szybkotnącej HSS-M2 (SW7M). Jeżeli natomiast oczekiwana jest wyższa trwałość międzyostrzeniowa lub części mają wyższą twardość > 20 HRC to przeciągacze wykonuje się ze stali szybkotnącej kobaltowej HSSe-M35 (HSS-Co, 5% kobaltu). Do twardszych część i/lub wstępnie utwardzonych zaleca się stal proszkową ASP30 lub S390 oraz dodatkowe pokrycia TiN, TiAlN lub Alcrona Pro.
Przeciągacze w przeciwieństwie do innych narzędzi skrawających ze względów kosztowych pokrywa się zazwyczaj tylko raz. Ponadto, jeżeli tolerancję są wąskie to po pokryciu należy przeostrzyć powierzchnię natarcia.
Przy twardościach części rzędu 35-40 HRC należy rozważyć użycie przeciągaczy z korpusem ze stali azotowanej oraz wkładkami węglikowymi. Pozostałe typy materiałów będą ulegały stępieniu bardzo szybko.

Rożne typy przeciągaczy, w tym przeciągacze do części o kształtach wewnętrznych i zewnętrznych
Zapraszamy do zapoznania się z naszą ofertą i innymi artykułami o obróbce kół zębatych, rowków wpustowych, wielowypustów ewolwentowych i pozostałych kształtów:
- Przeciągacze i przepychacze - oferta Tradensa - tutaj.
- Maszyny do przeciągania hydrauliczne i elektromechaniczne oraz oprzyrządowanie - tutaj.
- Przeciągacze i przepychacze - różnice w konstrukcji oraz obróbce - tutaj.
- Alternatywne dłutaki Fellowsa do obróbki kół zębatych i wielowypustów o uzębieniu wewnętrznym - tutaj.
- Artykuł o dłutakach Fellowsa - tutaj.
- Narzędzia do dłutowania rowków wpustowych, kwadratów, sześciokątów, kół zębatych i wielowypustów ewolwentowych i równoległych - tutaj.
W ofercie posiadamy m.in.
- przeciągacze i przepychacze do kół zębatych i wielowypustów
- przeciągacze i przepychacze wielowypustowe o zarysie ewolwentowym
- przeciągacze i przepychacze do rowków wpustowych, w tym również tulejki
- przeciągacze i przepychacze do kwadratów, pięciokątów i sześciokątów
- przeciągacze i przepychacze do profili specjalnych.
- przeciągacze i przepychacze do otworów cylindrycznych
- przeciągacze i przepychacze do otworów wielokątowych
- przeciągacze i przepychacze do otworów wielorowkowych prostokątnych
- przeciągacze i przepychacze do otworów wielorowkowych ewolwentowych
Do każdego zamówienia otrzymasz od nas pełne wsparcie techniczne oraz rysunek zamówionego przeciągacza lub przepychacza.